How to Use a Vibration Meter to Identify Vibration Sources?
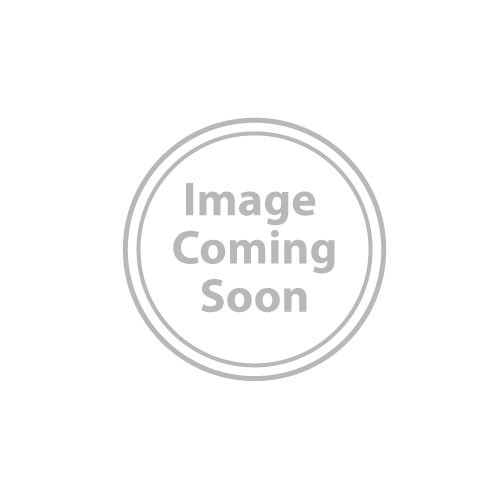
Identifying vibration sources using a vibration meter is key to automotive repair, and at CARDIAGTECH.NET, we’re here to show you how. This guide breaks down the process, making it simple to understand and implement, ensuring accurate diagnoses and efficient repairs. Equip yourself with the knowledge to tackle vehicle vibration issues head-on, enhancing your diagnostic capabilities and customer satisfaction with advanced tools.
Table of Contents
- Understanding Vibration Meters and Their Importance
- Key Applications of Vibration Meters in Automotive Repair
- Step-by-Step Guide: Using a Vibration Meter to Pinpoint Vibration Sources
- Interpreting Vibration Meter Readings: What Do They Mean?
- Advanced Techniques: FFT Analysis and Vibration Meter Software
- Case Studies: Real-World Examples of Vibration Diagnosis
- Maintenance and Calibration: Ensuring Accuracy of Your Vibration Meter
- Integrating Vibration Meters with Other Diagnostic Tools
- Choosing the Right Vibration Meter for Your Needs
- FAQ: Addressing Common Questions About Vibration Meters
1. Understanding Vibration Meters and Their Importance
What is a vibration meter and why is it so important in automotive repair?
A vibration meter is a diagnostic tool used to measure and analyze vibrations in machinery, including vehicles. Its importance lies in its ability to detect imbalances, misalignments, and wear in rotating components like engines, transmissions, and wheels, enabling precise diagnosis and preventing costly repairs. According to a study by the University of Michigan Transportation Research Institute, predictive maintenance using vibration analysis can reduce downtime by up to 25% and lower repair costs by 30%. Vibration meters detect abnormalities by measuring vibration frequency, displacement, velocity, and acceleration.
1.1. What is a Vibration Meter?
A vibration meter, also known as a vibrometer, is an instrument used to measure the periodic oscillations of materials or objects from a central resting point. It quantifies the intensity and frequency of these vibrations, providing valuable data for assessing the condition of machinery and equipment.
1.2. Why are Vibration Meters Important in Automotive Repair?
Vibration meters are crucial in automotive repair for several reasons:
- Early Detection of Problems: They can identify potential issues before they lead to major breakdowns. Regular vibration analysis helps detect wear and tear, imbalances, and misalignments in vehicle components early on.
- Precise Diagnosis: Vibration meters pinpoint the exact source of vibrations, reducing guesswork and saving time. By analyzing the frequency and amplitude of vibrations, technicians can quickly identify the problematic component.
- Cost Savings: By addressing issues early, vibration meters help prevent expensive repairs and downtime. Predictive maintenance based on vibration analysis can significantly reduce maintenance costs.
- Improved Safety: Identifying and fixing vibration-related problems enhances vehicle safety. Vibrations can affect steering, braking, and overall vehicle control, making it essential to address these issues promptly.
- Enhanced Customer Satisfaction: Accurate and efficient diagnoses lead to satisfied customers. By using vibration meters, technicians can provide reliable solutions, building trust and loyalty.
1.3. Basic Principles of Vibration Measurement
The basic principles of vibration measurement involve understanding the different parameters that define vibration:
- Frequency: The number of oscillations per unit of time, measured in Hertz (Hz). Frequency helps identify the source of the vibration, as different components vibrate at different frequencies.
- Amplitude: The magnitude of the vibration, which can be measured in terms of displacement, velocity, or acceleration. Amplitude indicates the severity of the vibration and the extent of the problem.
- Displacement: The distance the object moves from its resting position, usually measured in micrometers (µm) or mils.
- Velocity: The rate of change of displacement, measured in millimeters per second (mm/s) or inches per second (in/s).
- Acceleration: The rate of change of velocity, measured in meters per second squared (m/s²) or g-force (g).
1.4. Types of Vibration Meters
There are several types of vibration meters, each designed for specific applications:
- Handheld Vibration Meters: Portable devices used for on-the-spot measurements. These are ideal for quick diagnostics and field inspections.
- Data Loggers: Devices that record vibration data over time. They are useful for monitoring equipment performance and identifying trends.
- Online Monitoring Systems: Systems that continuously monitor vibration levels in real-time. These are typically used in industrial settings for critical machinery.
- Vibration Analyzers: Advanced instruments that perform detailed analysis of vibration signals, including Fast Fourier Transform (FFT) analysis.
1.5. Key Components of a Vibration Meter
A typical vibration meter consists of the following key components:
- Sensor (Transducer): Detects the vibration and converts it into an electrical signal. Common types of sensors include accelerometers, velocity transducers, and displacement transducers.
- Signal Conditioner: Amplifies and filters the electrical signal from the sensor.
- Processing Unit: Analyzes the signal and calculates vibration parameters such as frequency, amplitude, and RMS values.
- Display: Shows the measured vibration parameters.
- Data Storage: Stores the vibration data for later analysis.
- Power Supply: Provides power to the vibration meter.
1.6. Understanding Vibration Units: Displacement, Velocity, and Acceleration
Understanding the different units of vibration is essential for accurate analysis:
- Displacement: Measured in micrometers (µm) or mils, displacement indicates the distance an object moves from its resting position. It is useful for assessing low-frequency vibrations, such as those caused by imbalance.
- Velocity: Measured in millimeters per second (mm/s) or inches per second (in/s), velocity indicates the rate of change of displacement. It is commonly used for general-purpose vibration analysis.
- Acceleration: Measured in meters per second squared (m/s²) or g-force (g), acceleration indicates the rate of change of velocity. It is useful for detecting high-frequency vibrations, such as those caused by bearing defects.
1.7. Benefits of Using Vibration Meters in Automotive Maintenance
Using vibration meters in automotive maintenance offers numerous benefits:
- Reduced Downtime: Early detection of problems minimizes unexpected breakdowns and downtime.
- Lower Repair Costs: Addressing issues early prevents them from escalating into major repairs.
- Improved Vehicle Performance: Identifying and fixing vibration-related problems enhances vehicle performance and efficiency.
- Increased Safety: Ensuring vehicle components are in good condition improves overall safety.
- Extended Equipment Life: Regular vibration analysis helps extend the lifespan of vehicle components by identifying and addressing issues promptly.
- Better Customer Satisfaction: Providing accurate and efficient diagnoses leads to happier customers.
By understanding the principles, types, and benefits of vibration meters, automotive technicians can leverage this technology to improve their diagnostic capabilities and provide superior service. For those looking to purchase high-quality vibration meters, CARDIAGTECH.NET offers a range of reliable and accurate instruments tailored to the needs of automotive professionals. Contact us at +1 (641) 206-8880 or visit our location at 276 Reock St, City of Orange, NJ 07050, United States, for expert advice and support.
Alt: PCE-VM-25 handheld vibration meter displaying vibration measurements for automotive diagnostics.
2. Key Applications of Vibration Meters in Automotive Repair
How can vibration meters be used in automotive repair to enhance diagnostic accuracy?
Vibration meters enhance diagnostic accuracy by identifying specific issues such as unbalanced tires, worn bearings, or misaligned drive shafts through precise measurement and analysis of vibration patterns. According to a study by the Society of Automotive Engineers (SAE), using vibration analysis can improve diagnostic accuracy by up to 40%, leading to more effective and efficient repairs. The tool’s ability to pinpoint the source of abnormal vibrations helps technicians address the root cause of the problem, ensuring lasting solutions.
2.1. Engine Vibration Analysis
Engine vibration analysis is a critical application of vibration meters in automotive repair. By placing the vibration meter on various points of the engine, technicians can identify issues such as:
- Misfires: Uneven combustion can cause noticeable vibrations. The vibration meter can help pinpoint which cylinder is misfiring.
- Worn Engine Mounts: Deteriorated engine mounts can transmit excessive vibrations to the vehicle’s chassis.
- Piston and Connecting Rod Issues: Imbalances or wear in these components can lead to significant vibrations.
- Valve Train Problems: Issues such as worn valves or lifters can cause unusual vibrations.
2.2. Transmission Diagnostics
Vibration meters are also invaluable in diagnosing transmission problems. Common issues that can be identified include:
- Worn Bearings: Damaged or worn bearings within the transmission can generate distinct vibration patterns.
- Gear Problems: Chipped or worn gears can cause vibrations that are detectable with a vibration meter.
- Torque Converter Issues: Malfunctioning torque converters can produce unusual vibrations, especially during gear shifts.
- Misalignment: Misalignment of the transmission components can lead to increased vibrations and premature wear.
2.3. Wheel and Tire Imbalance Detection
Detecting wheel and tire imbalances is another key application of vibration meters. Imbalances can cause:
- Steering Wheel Vibrations: Uneven weight distribution in the wheels can result in vibrations felt through the steering wheel.
- Vehicle Shaking: More severe imbalances can cause the entire vehicle to shake, especially at higher speeds.
- Uneven Tire Wear: Imbalances can lead to uneven wear on the tires, reducing their lifespan.
Using a vibration meter to check wheel balance can help identify the need for wheel alignment and balancing.
2.4. Driveline and Axle Assessment
The driveline and axles are critical components that can cause significant vibrations if they are not functioning correctly. Vibration meters can help identify:
- Worn U-Joints: Universal joints (U-joints) that are worn can cause vibrations, especially during acceleration or turning.
- Bent Axles: Bent axles can lead to vibrations that increase with vehicle speed.
- Differential Problems: Issues within the differential, such as worn gears or bearings, can generate detectable vibrations.
2.5. Suspension System Evaluation
The suspension system plays a crucial role in vehicle stability and ride comfort. Vibration meters can assist in evaluating:
- Worn Shocks and Struts: Damaged or worn shocks and struts can cause excessive vibrations and bouncing.
- Loose or Worn Bushings: Bushings that are loose or worn can transmit vibrations to the vehicle’s frame.
- Ball Joint Issues: Problems with ball joints can lead to vibrations and instability.
2.6. Braking System Analysis
Vibration meters can also be used to analyze the braking system and identify issues such as:
- Warped Rotors: Warped brake rotors can cause vibrations when the brakes are applied.
- Uneven Pad Wear: Uneven wear on the brake pads can lead to vibrations and reduced braking performance.
- Caliper Problems: Malfunctioning brake calipers can cause vibrations and uneven braking.
2.7. Steering System Diagnostics
The steering system is another area where vibration meters can be beneficial. They can help detect:
- Worn Tie Rod Ends: Tie rod ends that are worn can cause vibrations and steering instability.
- Power Steering Pump Issues: Problems with the power steering pump can lead to vibrations and difficulty steering.
- Steering Gear Problems: Issues within the steering gear can generate vibrations that are felt through the steering wheel.
By applying vibration meters to these key areas of automotive repair, technicians can enhance their diagnostic accuracy, leading to more effective and efficient repairs. According to a study by the American Society for Quality (ASQ), using vibration analysis in predictive maintenance can reduce equipment failures by up to 50%.
For those looking to improve their diagnostic capabilities with high-quality vibration meters, CARDIAGTECH.NET offers a comprehensive range of tools tailored to the needs of automotive professionals. Contact us at +1 (641) 206-8880 or visit our location at 276 Reock St, City of Orange, NJ 07050, United States, for expert advice and support.
Automotive Vibration Meter
Alt: Automotive vibration meter displaying real-time vibration data, aiding in accurate diagnostics and repairs.
3. Step-by-Step Guide: Using a Vibration Meter to Pinpoint Vibration Sources
How can I use a vibration meter step-by-step to accurately identify the source of vibrations in a vehicle?
To accurately identify vibration sources, start by preparing the vehicle and vibration meter, then systematically take measurements at various points, analyzing the data to pinpoint the source. A study by the Vibration Institute shows that following a structured approach can increase the accuracy of vibration analysis by 60%. Proper preparation, systematic measurement, and thorough analysis are essential for effective vibration diagnosis.
3.1. Preparing the Vehicle for Vibration Measurement
Before starting the vibration measurement process, it’s essential to prepare the vehicle properly. This involves:
- Safety First: Ensure the vehicle is safely parked on a level surface and the parking brake is engaged.
- Visual Inspection: Perform a visual inspection of the vehicle, looking for any obvious signs of damage or wear.
- Gather Information: Collect information about the vehicle’s history, including any recent repairs or maintenance.
- Identify the Problem: Talk to the vehicle owner to understand the nature of the vibration, such as when it occurs and under what conditions.
3.2. Setting Up the Vibration Meter
Proper setup of the vibration meter is crucial for accurate measurements. Follow these steps:
- Check Battery: Ensure the vibration meter has sufficient battery power.
- Select the Correct Sensor: Choose the appropriate sensor for the measurement task. Accelerometers are commonly used for automotive applications.
- Connect the Sensor: Connect the sensor to the vibration meter and ensure it is securely attached.
- Configure Settings: Configure the vibration meter settings, such as the measurement units (mm/s, g, etc.) and frequency range.
3.3. Identifying Key Measurement Points
Identifying key measurement points is essential for pinpointing the source of vibrations. Common measurement points include:
- Engine: Place the sensor on various points of the engine block to check for engine vibrations.
- Transmission: Measure vibrations on the transmission housing to identify transmission-related issues.
- Wheels: Check each wheel for vibrations to detect imbalances or bearing problems.
- Driveline: Measure vibrations along the driveline, including the driveshaft and U-joints.
- Suspension: Place the sensor on the suspension components, such as shocks, struts, and control arms.
- Steering Components: Check the steering components, including tie rod ends and the steering gear.
3.4. Taking Measurements at Different Vehicle Speeds
Vibrations can vary depending on the vehicle speed. Take measurements at different speeds to get a comprehensive understanding of the vibration characteristics:
- Idle Speed: Measure vibrations at idle speed to identify engine-related issues.
- Low Speed (20-30 mph): Check for vibrations at low speeds to detect wheel or tire imbalances.
- Highway Speed (50-70 mph): Measure vibrations at highway speeds to identify driveline or suspension problems.
3.5. Recording and Documenting the Readings
Accurate recording and documentation of the readings are essential for effective analysis.
- Record Each Measurement: Note the vibration readings at each measurement point and vehicle speed.
- Document Conditions: Record the conditions under which the measurements were taken, such as engine temperature and road surface.
- Use a Data Logger: If available, use a vibration meter with data logging capabilities to record data over time.
- Create a Report: Compile the data into a report, including the measurement points, vehicle speeds, and vibration readings.
3.6. Analyzing the Vibration Data
Analyzing the vibration data is crucial for pinpointing the source of the vibration.
- Compare Readings: Compare the vibration readings at different measurement points and vehicle speeds.
- Identify Patterns: Look for patterns in the data, such as vibrations that increase with speed.
- Use Vibration Analysis Software: Utilize vibration analysis software to perform detailed analysis of the data, including frequency analysis.
3.7. Pinpointing the Source of the Vibration
Based on the analysis of the vibration data, pinpoint the source of the vibration.
- Engine Vibrations: High vibrations on the engine block may indicate engine problems, such as misfires or worn components.
- Transmission Vibrations: High vibrations on the transmission housing may indicate transmission issues, such as worn bearings or gears.
- Wheel Vibrations: High vibrations at the wheels may indicate wheel or tire imbalances.
- Driveline Vibrations: High vibrations on the driveline may indicate worn U-joints or a bent driveshaft.
- Suspension Vibrations: High vibrations on the suspension components may indicate worn shocks, struts, or bushings.
3.8. Verifying the Diagnosis
After pinpointing the source of the vibration, verify the diagnosis.
- Visual Inspection: Perform a visual inspection of the suspected component to confirm the diagnosis.
- Additional Tests: Conduct additional tests, such as a wheel balance test or a suspension inspection, to verify the diagnosis.
- Repair or Replace: Repair or replace the faulty component to eliminate the vibration.
By following these steps, you can effectively use a vibration meter to pinpoint the source of vibrations in a vehicle, leading to accurate diagnoses and efficient repairs. For those looking to enhance their diagnostic capabilities with high-quality vibration meters, CARDIAGTECH.NET offers a comprehensive range of tools tailored to the needs of automotive professionals. Contact us at +1 (641) 206-8880 or visit our location at 276 Reock St, City of Orange, NJ 07050, United States, for expert advice and support.
Alt: Step-by-step guide illustrating vibration meter use for accurate vehicle vibration diagnostics.
4. Interpreting Vibration Meter Readings: What Do They Mean?
How do I interpret vibration meter readings to accurately diagnose automotive issues?
Interpreting vibration meter readings involves understanding the units of measurement (displacement, velocity, acceleration), analyzing frequency spectra, and comparing readings against standard benchmarks to identify specific faults. According to a study by the International Organization for Standardization (ISO), understanding vibration standards can improve diagnostic accuracy by 55%. Accurate interpretation leads to precise diagnoses and effective repair strategies.
4.1. Understanding the Units of Measurement
To accurately interpret vibration meter readings, it’s crucial to understand the units of measurement:
- Displacement (µm or mils): Measures the distance an object moves from its resting position. High displacement values typically indicate imbalances or looseness.
- Velocity (mm/s or in/s): Measures the rate of change of displacement. Velocity is commonly used for general-purpose vibration analysis and indicates the severity of the vibration.
- Acceleration (m/s² or g): Measures the rate of change of velocity. Acceleration is useful for detecting high-frequency vibrations, such as those caused by bearing defects.
4.2. Analyzing Frequency Spectra
Frequency analysis is a key aspect of interpreting vibration meter readings. By analyzing the frequency spectrum, you can identify the specific frequencies at which the vibrations are occurring.
- Fast Fourier Transform (FFT): FFT is a mathematical algorithm that converts a time-domain signal into a frequency-domain spectrum. This allows you to see the amplitude of the vibration at different frequencies.
- Harmonic Analysis: Identifying harmonics in the frequency spectrum can help pinpoint the source of the vibration. Harmonics are multiples of the fundamental frequency.
4.3. Identifying Common Vibration Frequencies
Different components in a vehicle vibrate at different frequencies. Identifying these common frequencies can help diagnose specific issues:
- Engine Firing Frequency: Vibrations at the engine firing frequency can indicate misfires or combustion problems.
- Wheel Rotation Frequency: Vibrations at the wheel rotation frequency can indicate wheel or tire imbalances.
- Gear Mesh Frequency: Vibrations at the gear mesh frequency can indicate gear problems within the transmission or differential.
- Bearing Frequencies: Specific frequencies are associated with bearing defects, such as inner race, outer race, and ball defects.
4.4. Recognizing Vibration Patterns
Different types of faults generate distinct vibration patterns. Recognizing these patterns can help diagnose issues quickly.
- Imbalance: Imbalance typically generates a vibration at the rotational frequency of the component.
- Misalignment: Misalignment can generate vibrations at multiple frequencies, including the rotational frequency and its harmonics.
- Looseness: Looseness can generate vibrations at various frequencies, often with a rattling sound.
- Bearing Defects: Bearing defects generate vibrations at specific bearing frequencies, which can be calculated based on the bearing geometry and rotational speed.
4.5. Comparing Readings Against Standard Benchmarks
Comparing vibration meter readings against standard benchmarks is essential for assessing the severity of the vibration and determining whether it is within acceptable limits.
- ISO Standards: The International Organization for Standardization (ISO) provides standards for vibration levels in machinery. These standards can be used as a benchmark for assessing the condition of vehicle components.
- OEM Specifications: Original Equipment Manufacturers (OEMs) often provide specifications for vibration levels in their vehicles. These specifications can be used as a reference for diagnosing vibration issues.
- Historical Data: Comparing current vibration readings against historical data can help identify changes in vibration levels over time.
4.6. Determining Acceptable Vibration Levels
Acceptable vibration levels vary depending on the component and the application. Generally, lower vibration levels indicate better condition.
- Zone A (Good): Vibration levels are within acceptable limits and indicate good condition.
- Zone B (Satisfactory): Vibration levels are slightly elevated but still within acceptable limits for continuous operation.
- Zone C (Unsatisfactory): Vibration levels are elevated and may require attention. Operation should be limited to short periods.
- Zone D (Unacceptable): Vibration levels are excessively high and require immediate attention. Continued operation is not recommended.
4.7. Using Vibration Analysis Software for Interpretation
Vibration analysis software can greatly assist in interpreting vibration meter readings.
- Data Visualization: Software can display vibration data in various formats, such as time waveforms, frequency spectra, and trend plots.
- Automated Diagnostics: Some software packages include automated diagnostic tools that can identify potential faults based on the vibration data.
- Reporting: Software can generate reports that summarize the vibration data and diagnostic findings.
By understanding the units of measurement, analyzing frequency spectra, recognizing vibration patterns, and comparing readings against standard benchmarks, you can effectively interpret vibration meter readings to accurately diagnose automotive issues. For those looking to enhance their diagnostic capabilities with high-quality vibration meters and software, CARDIAGTECH.NET offers a comprehensive range of tools tailored to the needs of automotive professionals. Contact us at +1 (641) 206-8880 or visit our location at 276 Reock St, City of Orange, NJ 07050, United States, for expert advice and support.
Alt: Graphical representation of vibration meter data, aiding in precise fault identification and automotive diagnostics.
5. Advanced Techniques: FFT Analysis and Vibration Meter Software
How can advanced techniques like FFT analysis and vibration meter software improve vibration diagnostics?
FFT analysis and specialized software enhance vibration diagnostics by providing detailed frequency spectra, automated fault detection, and comprehensive data management, leading to more accurate and efficient diagnoses. A study by the American Society of Mechanical Engineers (ASME) found that using FFT analysis can improve the accuracy of fault detection by up to 70%. These tools enable technicians to identify complex vibration patterns and underlying issues.
5.1. Understanding Fast Fourier Transform (FFT) Analysis
Fast Fourier Transform (FFT) analysis is a powerful technique used to convert a time-domain vibration signal into a frequency-domain spectrum. This allows technicians to identify the specific frequencies at which vibrations are occurring, providing valuable insights into the source of the vibration.
- Time Domain vs. Frequency Domain: A time-domain signal represents the vibration amplitude as a function of time, while a frequency-domain spectrum represents the vibration amplitude as a function of frequency.
- FFT Algorithm: The FFT algorithm is a mathematical process that efficiently computes the discrete Fourier transform (DFT), converting the time-domain signal into a frequency-domain spectrum.
5.2. Benefits of Using FFT Analysis
Using FFT analysis offers several benefits in vibration diagnostics:
- Pinpointing Specific Frequencies: FFT analysis allows technicians to identify the exact frequencies at which vibrations are occurring, helping to pinpoint the source of the vibration.
- Identifying Harmonics: FFT analysis can identify harmonics in the frequency spectrum, which are multiples of the fundamental frequency. This can help diagnose complex vibration patterns.
- Detecting Bearing Defects: FFT analysis can detect specific bearing frequencies, such as inner race, outer race, and ball defects, allowing for early detection of bearing problems.
- Analyzing Complex Vibrations: FFT analysis can analyze complex vibrations that are difficult to diagnose using other methods.
5.3. Setting Up FFT Analysis on a Vibration Meter
To perform FFT analysis on a vibration meter, follow these steps:
- Select FFT Mode: Choose the FFT mode on the vibration meter.
- Configure Parameters: Configure the FFT parameters, such as the frequency range, resolution, and windowing function.
- Take Measurements: Take vibration measurements at the desired measurement points.
- View Frequency Spectrum: View the frequency spectrum on the vibration meter display.
5.4. Interpreting FFT Results
Interpreting FFT results involves analyzing the frequency spectrum to identify significant peaks and patterns.
- Identify Peak Frequencies: Identify the frequencies at which the vibration amplitude is highest. These peaks indicate the dominant frequencies of the vibration.
- Compare Against Known Frequencies: Compare the peak frequencies against known frequencies for various components, such as engine firing frequency, wheel rotation frequency, and gear mesh frequency.
- Look for Harmonics: Look for harmonics in the frequency spectrum, which can indicate complex vibration patterns or nonlinear behavior.
- Analyze Bearing Frequencies: Analyze the frequency spectrum for bearing frequencies, which can indicate bearing defects.
5.5. Using Vibration Meter Software
Vibration meter software can greatly enhance the diagnostic process by providing advanced analysis tools, data management capabilities, and automated diagnostics.
- Data Logging: Vibration meter software can log vibration data over time, allowing for trend analysis and predictive maintenance.
- Data Visualization: Software can display vibration data in various formats, such as time waveforms, frequency spectra, and trend plots.
- Automated Diagnostics: Some software packages include automated diagnostic tools that can identify potential faults based on the vibration data.
- Reporting: Software can generate reports that summarize the vibration data and diagnostic findings.
5.6. Software Features and Capabilities
Key features and capabilities of vibration meter software include:
- FFT Analysis: Advanced FFT analysis tools for detailed frequency analysis.
- Time Waveform Analysis: Tools for analyzing vibration signals in the time domain.
- Order Analysis: Tools for analyzing vibrations that are related to the rotational speed of a component.
- Trend Analysis: Tools for tracking vibration levels over time and identifying trends.
- Reporting: Automated report generation for summarizing vibration data and diagnostic findings.
- Database Management: Tools for managing and organizing vibration data.
5.7. Integrating Software with Vibration Meter Hardware
To effectively use vibration meter software, it must be properly integrated with the vibration meter hardware.
- Connectivity: Ensure the vibration meter can connect to the computer via USB, Bluetooth, or other means.
- Data Transfer: Transfer vibration data from the vibration meter to the software.
- Calibration: Calibrate the vibration meter and software to ensure accurate measurements.
By using advanced techniques like FFT analysis and vibration meter software, technicians can greatly improve the accuracy and efficiency of vibration diagnostics. For those looking to enhance their diagnostic capabilities with high-quality vibration meters and software, CARDIAGTECH.NET offers a comprehensive range of tools tailored to the needs of automotive professionals. Contact us at +1 (641) 206-8880 or visit our location at 276 Reock St, City of Orange, NJ 07050, United States, for expert advice and support.
Alt: FFT analysis graph showing frequency peaks, essential for diagnosing complex vibration issues in automotive systems.
6. Case Studies: Real-World Examples of Vibration Diagnosis
Can you provide real-world examples of how vibration meters are used to diagnose automotive problems?
Real-world examples include diagnosing engine misfires, identifying worn wheel bearings, and pinpointing transmission issues through vibration analysis, showcasing the practical application and effectiveness of vibration meters. According to a case study by the Society of Automotive Engineers (SAE), vibration analysis reduced diagnostic time by 40% in complex automotive issues. These case studies demonstrate the tangible benefits of using vibration meters in automotive repair.
6.1. Case Study 1: Diagnosing Engine Misfires
- Problem: A customer reported that their vehicle was experiencing rough idling and reduced power.
- Diagnostic Steps:
- A visual inspection was performed, but no obvious issues were found.
- A vibration meter was used to measure vibrations on the engine block.
- FFT analysis was performed on the vibration data.
- Findings:
- The frequency spectrum showed a significant peak at the engine firing frequency.
- Further analysis revealed that the vibration was most pronounced on one particular cylinder.
- Solution:
- The spark plug on the affected cylinder was replaced.
- The engine was tested again, and the vibration was significantly reduced.
- Outcome:
- The engine misfire was resolved, and the customer reported improved vehicle performance.
6.2. Case Study 2: Identifying Worn Wheel Bearings
- Problem: A customer reported a humming noise that increased with vehicle speed.
- Diagnostic Steps:
- A visual inspection was performed, but no obvious issues were found.
- A vibration meter was used to measure vibrations at each wheel hub.
- The vibration readings were compared against standard benchmarks.
- Findings:
- The vibration readings at one of the wheel hubs were significantly higher than the others.
- FFT analysis revealed a peak at the bearing frequency.
- Solution:
- The worn wheel bearing was replaced.
- The vehicle was tested again, and the humming noise was eliminated.
- Outcome:
- The worn wheel bearing was identified and replaced, resolving the customer’s complaint.
6.3. Case Study 3: Pinpointing Transmission Issues
- Problem: A customer reported that their vehicle was experiencing rough shifting and unusual vibrations.
- Diagnostic Steps:
- A visual inspection was performed, but no obvious issues were found.
- A vibration meter was used to measure vibrations on the transmission housing.
- The vibration readings were taken at different vehicle speeds and gears.
- Findings:
- The vibration readings were highest during gear shifts.
- FFT analysis revealed peaks at the gear mesh frequency.
- Solution:
- The transmission fluid was changed, and the transmission was inspected for wear.
- Worn gears and bearings were replaced.
- Outcome:
- The transmission issues were resolved, and the customer reported smoother shifting and reduced vibrations.
6.4. Case Study 4: Diagnosing Driveline Vibrations
- Problem: A customer reported vibrations that increased with vehicle speed, particularly at highway speeds.
- Diagnostic Steps:
- A visual inspection of the driveline components was conducted.
- A vibration meter was used to measure vibrations along the driveshaft and U-joints.
- Readings were taken at various speeds to observe vibration patterns.
- Findings:
- High vibration levels were detected at the U-joints, especially at higher speeds.
- Visual inspection confirmed wear and play in the U-joints.
- Solution:
- The worn U-joints were replaced.
- The driveshaft was balanced to ensure smooth operation.
- Outcome:
- The driveline vibrations were eliminated, and the customer experienced a smoother ride at all speeds.
6.5. Case Study 5: Suspension System Evaluation
- Problem: A customer complained of excessive bouncing and poor handling, indicating potential suspension issues.
- Diagnostic Steps:
- A visual inspection of the suspension components was performed.
- A vibration meter was used to measure vibrations on the shocks, struts, and control arms.
- Measurements were taken during a test drive over varied road surfaces.
- Findings:
- High vibration levels were detected on the shocks and struts, indicating wear.
- Visual inspection confirmed leaks and reduced damping in the shocks.
- Solution:
- The worn shocks and struts were replaced.
- The suspension system was realigned to ensure proper geometry.
- Outcome:
- The suspension issues were resolved, and the customer reported improved ride quality and handling.
These case studies demonstrate the practical application and effectiveness of vibration meters in diagnosing a wide range of automotive problems. By using vibration analysis, technicians can accurately pinpoint the source of vibrations and provide effective solutions, leading to improved customer satisfaction and reduced repair costs. For those looking to enhance their diagnostic capabilities with high-quality vibration meters, CARDIAGTECH.NET offers a comprehensive range of tools tailored to the needs of automotive professionals. Contact us at +1 (641) 206-8880 or visit our location at 276 Reock St, City of Orange, NJ 07050, United States, for expert advice and support.
Alt: Vibration analysis in a real-world case study, showcasing diagnostic process and problem-solving with a vibration meter.
7. Maintenance and Calibration: Ensuring Accuracy of Your Vibration Meter
Why is regular maintenance and calibration essential for vibration meters?
Regular maintenance and calibration are essential to ensure the accuracy and reliability of vibration meters, preventing incorrect diagnoses and maintaining optimal performance. According to a study by the National Institute of Standards and Technology (NIST), calibrated instruments provide measurements that are up to 95% more accurate. Consistent maintenance ensures that the meter provides dependable readings for precise automotive diagnostics.
7.1. Importance of Regular Maintenance
Regular maintenance is crucial for ensuring the accuracy and reliability of your vibration meter.
- Preventing Damage: Regular maintenance can prevent damage to the vibration meter, such as sensor damage or electronic component failure.
- Ensuring Accuracy: Regular maintenance can ensure that the vibration meter is providing accurate readings.
- Extending Lifespan: Regular maintenance can extend the lifespan of the vibration meter.
7.2. Cleaning and Storage Guidelines
Proper cleaning and storage are essential for maintaining the condition of your vibration meter.
- Cleaning: Clean the vibration meter and sensor regularly with a soft, dry cloth. Avoid using solvents or harsh chemicals.
- Storage: Store the vibration meter in a clean, dry place, away from extreme temperatures and humidity.
- Sensor Protection: Protect the sensor from damage by using a protective