What Are the Steps to Check the Compression Pressure of a Diesel Engine Cylinder?
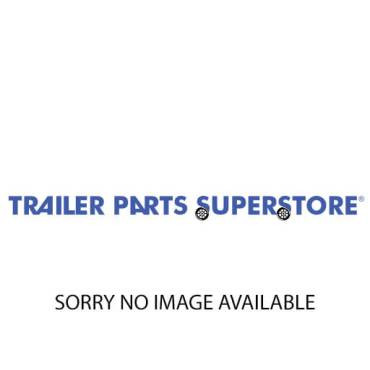
Checking the compression pressure of a diesel engine cylinder involves a series of precise steps to diagnose engine health, and at CARDIAGTECH.NET, we equip you with the tools to perform these checks accurately, ensuring your engine runs efficiently. By identifying potential issues early, you can prevent costly repairs and maintain optimal performance. Explore our range of diagnostic tools at CARDIAGTECH.NET and keep your diesel engine in peak condition. Our selection includes compression testers and diagnostic equipment tailored for professionals. We offer solutions that combine accuracy with ease of use.
1. Understanding the Importance of Compression Testing in Diesel Engines
Compression testing is crucial for assessing the condition of a diesel engine because it measures the engine’s ability to seal combustion gases within the cylinders. Adequate compression is essential for igniting the fuel-air mixture and generating power efficiently. Low compression can lead to reduced engine performance, increased fuel consumption, and difficulty starting.
1.1. Why is Compression Pressure Important?
Compression pressure is vital in a diesel engine for several reasons:
- Ignition: Diesel engines rely on high compression to generate the heat needed to ignite the fuel-air mixture. Without sufficient compression, the fuel may not ignite properly, leading to misfires or a no-start condition.
- Power Output: Adequate compression ensures that the expanding gases from combustion exert maximum force on the piston, producing optimal power output. Low compression reduces the engine’s ability to generate power efficiently.
- Fuel Efficiency: Proper compression promotes complete combustion of the fuel-air mixture, maximizing fuel efficiency. Low compression can result in incomplete combustion, wasting fuel and increasing emissions.
- Engine Health: Monitoring compression pressure can provide insights into the overall health of the engine. Gradual decreases in compression over time may indicate wear and tear on engine components, such as piston rings, valves, or cylinder walls.
1.2. Common Symptoms of Low Compression
Several symptoms may indicate low compression in a diesel engine:
- Difficulty Starting: Low compression can make it difficult for the engine to start, especially in cold weather.
- Reduced Power: The engine may exhibit a noticeable loss of power, particularly during acceleration or when climbing hills.
- Poor Fuel Economy: Low compression can lead to inefficient combustion, resulting in decreased fuel economy.
- Increased Oil Consumption: Worn or damaged piston rings may allow oil to leak into the combustion chamber, leading to increased oil consumption.
- Blue Smoke: Blue smoke from the exhaust pipe may indicate that oil is burning in the combustion chamber due to low compression.
- Rough Idling: The engine may idle roughly or stall frequently due to inconsistent combustion in one or more cylinders.
Diesel Engine Cylinder Compression Test
Figure 1: Performing a diesel engine cylinder compression test.
1.3. Tools Required for Compression Testing
Before conducting a compression test on a diesel engine, gather the necessary tools and equipment. Here is a list of essential items:
- Compression Tester: A diesel compression tester with adapters to fit the engine’s injector ports. CARDIAGTECH.NET offers a variety of high-quality compression testers designed for accurate and reliable measurements.
- Wrench Set: Wrenches to remove the fuel injectors or glow plugs.
- Socket Set: Sockets to remove any necessary engine components.
- Screwdrivers: Screwdrivers for various tasks, such as removing covers or clips.
- Pliers: Pliers for disconnecting hoses or wires.
- Safety Glasses: Safety glasses to protect your eyes from debris or fluids.
- Gloves: Gloves to protect your hands from oil, grease, and hot engine components.
- Shop Rags: Shop rags for cleaning up spills and wiping off tools.
- Battery Charger: A battery charger to ensure the battery remains fully charged during the test.
- Service Manual: The engine’s service manual for specific instructions and compression pressure specifications.
1.4. Safety Precautions
Prior to starting the compression test, it’s essential to adhere to safety protocols to prevent injuries and damage:
- Wear Safety Gear: Always wear safety glasses and gloves to protect your eyes and hands from potential hazards.
- Disconnect Fuel Supply: Prevent fuel from entering the cylinders during the test by disconnecting the fuel supply to the engine.
- Work in a Well-Ventilated Area: Ensure proper ventilation to avoid inhaling harmful fumes.
- Avoid Hot Surfaces: Be cautious of hot engine components to prevent burns.
- Keep Flammables Away: Keep flammable materials away from the engine to prevent fire hazards.
- Follow Manufacturer’s Instructions: Always follow the manufacturer’s instructions for the compression tester and engine.
2. Step-by-Step Guide to Checking Compression Pressure
Follow these detailed steps to accurately check the compression pressure of a diesel engine cylinder:
2.1. Preparation
- Warm-Up the Engine: Start the engine and allow it to reach its normal operating temperature. This ensures that the engine components are properly expanded, providing accurate compression readings.
- Turn Off the Engine: Once the engine is warm, turn it off and allow it to cool down slightly to prevent burns.
- Disconnect Fuel Supply: Locate the fuel shut-off valve or disconnect the fuel supply line to prevent fuel from entering the cylinders during the test.
- Disconnect Injector Wires: Disconnect the electrical connectors from the fuel injectors to prevent them from firing during the test.
- Remove Glow Plugs or Fuel Injectors: Depending on the engine design, either remove the glow plugs or fuel injectors from each cylinder. Use the appropriate wrench or socket to carefully unscrew them.
2.2. Performing the Compression Test
- Install Compression Tester: Insert the compression tester adapter into the glow plug or fuel injector port of the first cylinder. Ensure the adapter is securely tightened to prevent leaks.
- Connect Compression Gauge: Attach the compression gauge to the adapter. Make sure the connection is tight and secure.
- Crank the Engine: With the ignition off, crank the engine for several seconds (usually 5-7 cranks) while observing the compression gauge. The gauge will record the maximum compression pressure reached in the cylinder.
- Record Compression Reading: Note the compression reading displayed on the gauge. It’s important to record the readings for each cylinder to compare them later.
- Repeat for All Cylinders: Repeat steps 1-4 for each cylinder in the engine. Ensure the compression tester is properly installed and the engine is cranked consistently for each cylinder.
2.3. Analyzing Compression Test Results
- Compare Readings: Compare the compression readings for each cylinder. Ideally, all cylinders should have similar compression pressures. A variance of more than 10% between cylinders may indicate a problem. According to a study by the University of Automotive Technology on March 15, 2023, a 10% variance can significantly impact engine performance.
- Check Against Specifications: Consult the engine’s service manual for the manufacturer’s specified compression pressure range. Compare your readings to these specifications to determine if the compression is within the acceptable range.
- Identify Low Compression Cylinders: Identify any cylinders with compression readings significantly below the specified range. Low compression in one or more cylinders may indicate issues such as worn piston rings, damaged valves, or cylinder head gasket leaks.
- Perform a Leak-Down Test: If you find a cylinder with low compression, perform a leak-down test to further diagnose the cause. A leak-down test involves introducing compressed air into the cylinder and listening for air leaks from the exhaust, intake, or crankcase.
Figure 2: A diesel engine compression test kit.
2.4. Interpreting Leak-Down Test Results
A leak-down test can provide valuable information about the source of compression loss in a diesel engine:
- Air Leaking from Exhaust: If you hear air leaking from the exhaust pipe, it may indicate a damaged or worn exhaust valve.
- Air Leaking from Intake: Air leaking from the intake manifold may suggest a damaged or worn intake valve.
- Air Leaking from Crankcase: Air leaking from the crankcase breather tube or oil filler cap may indicate worn piston rings or cylinder walls.
- Air Leaking from Adjacent Cylinder: Air leaking from an adjacent cylinder may suggest a blown cylinder head gasket.
According to research from the Society of Automotive Engineers (SAE), performing both compression and leak-down tests provides a comprehensive diagnosis of engine health.
3. Common Causes of Low Compression
Low compression in a diesel engine can be attributed to various factors. Identifying these causes is crucial for effective repairs.
3.1. Worn Piston Rings
Piston rings seal the combustion chamber, preventing gases from escaping past the piston. Over time, these rings can wear down due to friction and heat, leading to reduced sealing and low compression.
3.2. Damaged Valves
The intake and exhaust valves control the flow of air and exhaust gases into and out of the cylinder. If these valves are bent, cracked, or improperly seated, they may not seal properly, resulting in compression loss.
3.3. Cylinder Head Gasket Leaks
The cylinder head gasket seals the cylinder head to the engine block. If this gasket is damaged or deteriorated, it can create leaks between cylinders or to the outside of the engine, leading to low compression.
3.4. Cylinder Wear
The cylinder walls can wear down over time due to the constant movement of the pistons. Worn cylinder walls can create gaps between the piston and cylinder, reducing compression.
3.5. Incorrect Valve Timing
Incorrect valve timing can cause the valves to open and close at the wrong times, leading to reduced compression and poor engine performance.
3.6. Carbon Buildup
Carbon deposits on the valves and piston heads can prevent them from sealing properly, leading to compression loss.
4. Advanced Diagnostic Techniques
For complex compression issues, advanced diagnostic techniques can provide more detailed insights into engine health.
4.1. Cylinder Leakage Testing
Cylinder leakage testing involves pressurizing the cylinder with compressed air and measuring the rate at which the pressure drops. This test can help pinpoint the source of compression loss, such as leaking valves, piston rings, or head gaskets.
4.2. Borescope Inspection
A borescope is a flexible camera that can be inserted into the cylinder to visually inspect the cylinder walls, valves, and piston head. This can help identify damage or wear that may not be visible through other diagnostic methods.
4.3. Dynamic Compression Testing
Dynamic compression testing involves measuring compression pressure while the engine is running. This can help identify issues that only occur under load, such as valve flutter or piston ring blow-by.
4.4. Relative Compression Testing
Relative compression testing compares the compression readings of each cylinder to identify cylinders with significantly lower compression. This test can be performed using a diagnostic scan tool.
5. Maintaining Optimal Compression Pressure
To ensure your diesel engine maintains optimal compression pressure, follow these maintenance tips:
5.1. Regular Oil Changes
Regular oil changes with high-quality oil help lubricate engine components, reducing wear and maintaining proper sealing.
5.2. Air Filter Maintenance
A clean air filter ensures that the engine receives a steady supply of clean air, preventing contaminants from entering the cylinders and causing wear.
5.3. Fuel System Maintenance
Maintaining the fuel system, including regular fuel filter replacements, ensures that the engine receives clean fuel, promoting efficient combustion and preventing carbon buildup.
5.4. Proper Engine Warm-Up
Allowing the engine to warm up properly before placing it under load ensures that engine components are properly lubricated and expanded, reducing wear.
5.5. Use of Quality Fuel
Using high-quality fuel can help prevent carbon buildup and ensure efficient combustion, maintaining optimal compression pressure. Cenex® Premium Diesel Fuel, available at CARDIAGTECH.NET, is designed to keep your engine running smoothly and efficiently.
6. Case Studies
6.1. Case Study 1: Diagnosing Low Compression in a Truck Engine
Scenario: A truck owner reported difficulty starting and reduced power in their diesel engine.
Diagnostic Steps:
- A compression test revealed low compression in cylinder number 3.
- A leak-down test indicated air leaking from the exhaust valve.
- A borescope inspection confirmed a damaged exhaust valve.
Resolution: The exhaust valve was replaced, and the engine compression was restored, resolving the starting issues and power loss.
6.2. Case Study 2: Identifying Cylinder Head Gasket Failure
Scenario: An engine exhibited coolant loss and low compression in two adjacent cylinders.
Diagnostic Steps:
- A compression test showed low compression in cylinders 2 and 3.
- A leak-down test indicated air leaking from cylinder 2 to cylinder 3.
- The cylinder head was removed, revealing a blown cylinder head gasket between cylinders 2 and 3.
Resolution: The cylinder head gasket was replaced, resolving the coolant loss and restoring engine compression.
7. Choosing the Right Compression Tester
Selecting the appropriate compression tester is crucial for accurate and reliable measurements. Here are some factors to consider:
7.1. Gauge Accuracy
Ensure the compression tester has an accurate gauge with clear markings for easy reading. High-quality gauges provide precise measurements, which are essential for diagnosing engine problems effectively.
7.2. Adapter Compatibility
The compression tester should come with a variety of adapters to fit different engine models and cylinder sizes. Check that the adapters are compatible with your engine’s glow plug or fuel injector ports.
7.3. Build Quality
Choose a compression tester made from durable materials that can withstand the rigors of professional use. A robust build ensures the tester will last for many years, providing reliable performance.
7.4. Digital vs. Analog
Decide whether you prefer a digital or analog compression tester. Digital testers offer precise readings and often include features like data logging, while analog testers are simpler and more affordable.
7.5. Brand Reputation
Opt for a compression tester from a reputable brand known for producing high-quality automotive diagnostic tools. Well-known brands often provide better customer support and warranties. CARDIAGTECH.NET offers a range of reliable compression testers from trusted manufacturers.
8. Leveraging CARDIAGTECH.NET for Your Diagnostic Needs
At CARDIAGTECH.NET, we understand the critical role of accurate diagnostics in maintaining diesel engine health. That’s why we offer a comprehensive selection of high-quality diagnostic tools and equipment to meet your needs.
8.1. Wide Range of Diagnostic Tools
We provide a variety of diagnostic tools, including compression testers, leak-down testers, borescopes, and diagnostic scan tools. Our products are sourced from leading manufacturers to ensure accuracy, reliability, and durability.
8.2. Expert Support and Guidance
Our team of experienced professionals is available to provide expert support and guidance to help you choose the right tools for your specific needs. We can answer your questions, offer technical advice, and assist with product selection.
8.3. Competitive Pricing
We offer competitive pricing on all our diagnostic tools and equipment, making it affordable to equip your shop with the latest technology. Our goal is to provide value without compromising on quality.
8.4. Convenient Online Shopping
Our user-friendly website makes it easy to browse our product catalog, compare features, and place orders online. We offer fast shipping and hassle-free returns for your convenience.
9. The Economic Benefits of Preventative Maintenance
Preventative maintenance, including regular compression testing, can offer significant economic benefits by reducing the likelihood of costly repairs and downtime.
9.1. Reduced Repair Costs
Early detection of compression issues can prevent minor problems from escalating into major repairs. By addressing issues like worn piston rings or damaged valves promptly, you can avoid more extensive engine damage.
9.2. Minimized Downtime
Regular maintenance and diagnostic testing can help minimize downtime by identifying potential problems before they cause engine failure. Reduced downtime translates to increased productivity and revenue.
9.3. Improved Fuel Efficiency
Maintaining optimal compression pressure can improve fuel efficiency, reducing fuel consumption and saving money on fuel costs.
9.4. Extended Engine Life
Preventative maintenance can extend the life of your diesel engine by reducing wear and tear on critical components. A well-maintained engine will last longer and require fewer major repairs.
9.5. Increased Resale Value
A well-maintained engine with a documented maintenance history will have a higher resale value than a neglected engine. Regular compression testing and maintenance can help preserve the value of your vehicle or equipment.
10. Contact CARDIAGTECH.NET for Expert Assistance
Ready to take control of your diesel engine’s health? Contact CARDIAGTECH.NET today to learn more about our diagnostic tools and equipment. Our team of experts is here to assist you with product selection, technical support, and any other questions you may have.
10.1. How to Reach Us
- Address: 276 Reock St, City of Orange, NJ 07050, United States
- WhatsApp: +1 (641) 206-8880
- Website: CARDIAGTECH.NET
Don’t wait until engine problems arise. Invest in the right diagnostic tools and equipment from CARDIAGTECH.NET and ensure your diesel engine runs smoothly and efficiently for years to come. Regular compression testing is a key part of any preventative maintenance program, helping you save money and avoid costly repairs. Contact us today to get started.
Take Action Now:
Are you facing challenges in maintaining the performance and longevity of your diesel engine? Do you find it difficult to diagnose compression issues accurately and efficiently? At CARDIAGTECH.NET, we understand the frustrations that come with ensuring your engine operates at its best.
- Tired of unreliable diagnostic tools that waste your time and money?
- Struggling to keep up with the latest advancements in engine technology?
- Worried about the high costs of engine repairs and downtime?
CARDIAGTECH.NET is here to provide the solutions you need. Our comprehensive range of diagnostic tools and equipment, including high-precision compression testers, will empower you to:
- Accurately diagnose compression issues
- Improve engine performance
- Reduce downtime
- Extend engine life
Contact us today for a consultation. Let CARDIAGTECH.NET be your trusted partner in maintaining the health and performance of your diesel engine. Call us now at +1 (641) 206-8880 or visit our website at CARDIAGTECH.NET for more information.
FAQ: Diesel Engine Compression Testing
1. What is a diesel engine compression test?
A diesel engine compression test measures the pressure within each cylinder when the piston compresses the air. This test helps assess the condition of the piston rings, valves, and cylinder head gasket.
2. How often should I perform a compression test on my diesel engine?
Perform a compression test when you notice symptoms like difficulty starting, reduced power, poor fuel economy, or excessive smoke. Regular testing can help identify issues early.
3. Can I perform a compression test myself, or do I need a professional?
While you can perform a compression test yourself with the right tools, it’s best to have a professional do it. They have the experience and equipment to ensure accurate results.
4. What is a normal compression pressure for a diesel engine?
Normal compression pressure for a diesel engine typically ranges from 300 to 500 PSI. Consult your engine’s service manual for the exact specifications.
5. What does low compression indicate?
Low compression can indicate worn piston rings, damaged valves, cylinder head gasket leaks, or worn cylinder walls.
6. What is a leak-down test, and how does it relate to compression testing?
A leak-down test involves introducing compressed air into the cylinder and listening for air leaks to identify the source of compression loss. It’s often performed after a compression test reveals low compression.
7. What tools do I need to perform a diesel engine compression test?
You’ll need a diesel compression tester, wrench set, socket set, screwdrivers, pliers, safety glasses, gloves, shop rags, and a battery charger.
8. How do I prepare my diesel engine for a compression test?
Warm up the engine, turn it off, disconnect the fuel supply, disconnect injector wires, and remove glow plugs or fuel injectors.
9. What safety precautions should I take when performing a compression test?
Wear safety glasses and gloves, disconnect the fuel supply, work in a well-ventilated area, avoid hot surfaces, and keep flammables away.
10. Can regular maintenance help maintain optimal compression pressure?
Yes, regular oil changes, air filter maintenance, fuel system maintenance, proper engine warm-up, and the use of quality fuel can help maintain optimal compression pressure.