Do You Conduct Occupational Safety Training Sessions for Employees?
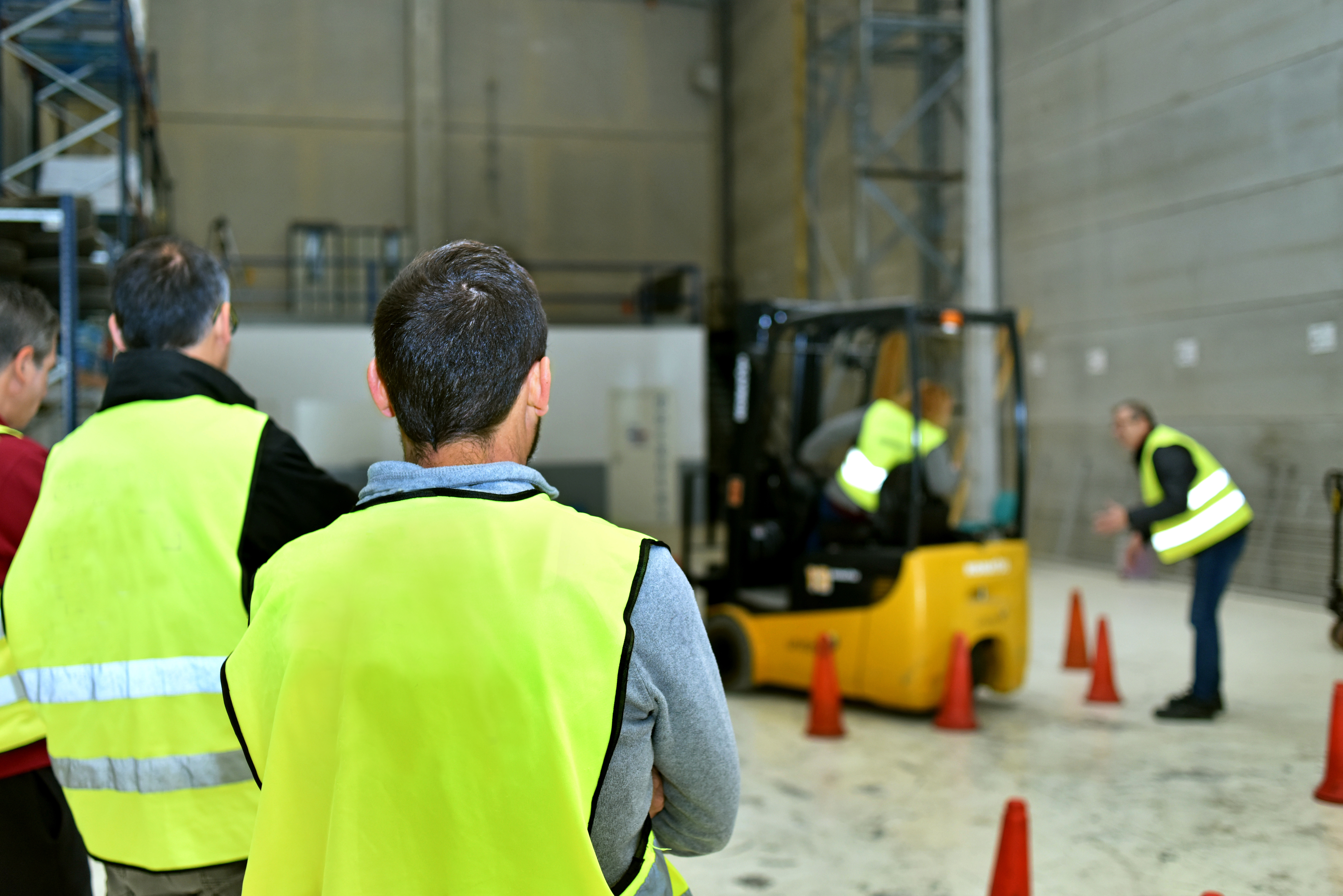
Do you conduct occupational safety training sessions for employees? Yes, CARDIAGTECH.NET understands the critical importance of occupational safety training for employees. Through comprehensive safety programs, businesses can drastically reduce workplace accidents, enhance productivity, and cultivate a culture of safety awareness. This ultimately leads to a more engaged and secure workforce. Let’s explore the benefits of safety training, the components of effective programs, and how CARDIAGTECH.NET can assist you in creating a safer work environment. These programs boost employee morale, improve company image and reduce insurance costs.
1. Understanding the Importance of Occupational Safety Training
Why is occupational safety training so crucial?
Occupational safety training equips employees with the knowledge and skills necessary to identify hazards, mitigate risks, and prevent accidents in the workplace. According to the Occupational Safety and Health Administration (OSHA), effective safety training can reduce injuries and illnesses by 25% to 30%. This not only protects employees but also significantly reduces costs associated with workers’ compensation, medical expenses, and lost productivity.
1.1. Benefits of Comprehensive Safety Training
What are the key benefits of investing in comprehensive safety training?
- Reduced Workplace Accidents and Injuries: Training helps employees recognize and avoid potential hazards.
- Increased Productivity: A safer work environment reduces downtime and increases efficiency.
- Improved Employee Morale: Employees feel valued and protected, leading to higher job satisfaction.
- Compliance with Regulations: Training ensures adherence to OSHA and other regulatory requirements.
- Lower Costs: Reduced accidents translate to lower insurance premiums and workers’ compensation claims.
1.2. The Cost of Neglecting Safety Training
What are the potential consequences of neglecting occupational safety training?
Consequence | Description |
---|---|
Legal Penalties | Failure to comply with OSHA regulations can result in significant fines and legal repercussions. According to OSHA, serious violations can result in penalties of up to $14,502 per violation. Repeat or willful violations can lead to fines of up to $145,027 per violation. |
Increased Costs | Workplace accidents lead to increased workers’ compensation claims, medical expenses, and lost productivity. The National Safety Council estimates that workplace injuries cost businesses billions of dollars annually. |
Damaged Reputation | Accidents and safety violations can tarnish a company’s reputation, making it difficult to attract and retain talent. |
Decreased Morale | A lack of safety training can create a culture of fear and anxiety among employees, leading to decreased morale and higher turnover rates. |
Loss of Productivity | Workplace accidents result in downtime and disruptions to operations, leading to decreased productivity and missed deadlines. |
2. Key Components of an Effective Safety Training Program
What elements should be included in a comprehensive safety training program?
A well-designed safety training program should be tailored to the specific needs of the workplace, address potential hazards, and incorporate interactive and engaging training methods. It should also be regularly evaluated and updated to ensure its effectiveness.
2.1. Hazard Identification and Risk Assessment
How do you identify potential hazards in the workplace?
- Job Safety Analysis (JSA): A JSA involves a team effort to investigate work areas and identify potential hazards associated with each job and operation. According to OSHA, a JSA should not only identify hazards but also prioritize them using the hierarchy of controls, which emphasizes eliminating hazards entirely as the best course of action, followed by substitution, engineering controls, work practice controls, and finally, personal protective equipment (PPE) as the last resort.
- Workplace Inspections: Regular inspections help identify unsafe conditions and behaviors.
- Incident Reporting: Encourage employees to report near misses and accidents to identify trends and prevent future incidents.
2.2. Training Content and Delivery Methods
What training methods are most effective for different learning styles?
- Lectures and Presentations: Provide foundational knowledge and information.
- Hands-On Training: Allow employees to practice safety procedures in a controlled environment.
- Group Discussions: Encourage participation and knowledge sharing.
- Visual Aids: Use images, videos, and animations to illustrate safety concepts.
- Simulations: Create realistic scenarios to test employees’ ability to respond to emergencies.
2.3. Regular Evaluation and Updates
How do you ensure your safety training program remains effective?
- Gather Feedback: Collect feedback from participants through surveys, focus groups, or anonymous polls.
- Analyze Training Data: Track safety metrics such as incident rates, near misses, and employee participation in safety programs.
- Review and Update: Regularly review and update training materials and delivery methods to ensure they remain relevant and effective.
Safety Training Session
3. Tailoring Safety Training to Specific Industries
How should safety training be customized for different industries?
Safety training should be tailored to the specific hazards and risks associated with each industry. For example, construction workers require training on fall protection and heavy equipment operation, while healthcare workers need training on infection control and hazardous materials handling.
3.1. Automotive Repair Industry
What are the specific safety considerations for automotive repair shops?
- Hazardous Materials Handling: Training on the safe handling and disposal of chemicals, solvents, and automotive fluids.
- Equipment Operation: Training on the safe operation of lifts, jacks, and other garage equipment.
- Personal Protective Equipment (PPE): Proper use of safety glasses, gloves, and respirators.
- Confined Space Entry: Training on the hazards of working in confined spaces such as fuel tanks.
3.2. Construction Industry
What are the essential safety training topics for construction workers?
- Fall Protection: Training on the use of harnesses, guardrails, and safety nets. According to OSHA, falls are the leading cause of death in the construction industry, accounting for more than one-third of all construction fatalities.
- Trenching and Excavation Safety: Training on the hazards of trench collapse and proper shoring techniques.
- Electrical Safety: Training on the dangers of working with electricity and proper lockout/tagout procedures.
- Heavy Equipment Operation: Training on the safe operation of bulldozers, excavators, and other heavy machinery.
3.3. Healthcare Industry
What safety measures are critical for healthcare professionals?
- Infection Control: Training on hand hygiene, personal protective equipment, and proper disposal of medical waste. The Centers for Disease Control and Prevention (CDC) estimates that healthcare-associated infections (HAIs) affect millions of patients each year.
- Hazardous Materials Handling: Training on the safe handling and disposal of chemicals, medications, and other hazardous materials.
- Patient Handling: Training on proper lifting techniques to prevent musculoskeletal injuries.
- Emergency Response: Training on how to respond to medical emergencies and other disasters.
4. Leveraging Technology for Effective Safety Training
How can technology enhance safety training programs?
Technology offers a variety of tools and platforms that can enhance the effectiveness of safety training, making it more engaging, accessible, and cost-effective.
4.1. Online Training Platforms
What are the advantages of using online training platforms?
- Accessibility: Employees can access training materials anytime, anywhere.
- Cost-Effectiveness: Online training reduces the need for in-person instructors and travel expenses.
- Engagement: Interactive modules, videos, and quizzes can make training more engaging and memorable.
- Tracking: Online platforms allow you to track employee progress and compliance.
4.2. Virtual Reality (VR) and Augmented Reality (AR)
How can VR and AR be used to improve safety training?
- Realistic Simulations: VR and AR can create realistic simulations of hazardous environments, allowing employees to practice safety procedures in a safe and controlled setting. A study by the National Training and Simulation Association found that VR training can improve knowledge retention by up to 80%.
- Interactive Learning: VR and AR can provide interactive learning experiences that engage employees and improve their understanding of safety concepts.
- Risk-Free Training: VR and AR allow employees to make mistakes and learn from them without risking real-world consequences.
4.3. Mobile Apps
How can mobile apps support safety training efforts?
- Accessibility: Employees can access safety information and training materials on their smartphones or tablets.
- Real-Time Updates: Mobile apps can provide real-time updates on safety procedures and regulations.
- Reporting: Employees can use mobile apps to report hazards and incidents from the field.
- Checklists: Safety checklists can be easily accessed and completed via mobile apps, ensuring all necessary precautions are taken before starting a task.
5. Addressing Common Challenges in Safety Training
What are some common obstacles to effective safety training, and how can they be overcome?
Implementing a successful safety training program can present several challenges. Here are some common obstacles and strategies for overcoming them:
5.1. Lack of Employee Engagement
How do you make safety training more engaging and relevant?
- Tailor Training to Specific Roles: Customize training content to address the specific hazards and risks associated with each employee’s job.
- Use Interactive Methods: Incorporate group discussions, case studies, and hands-on activities to encourage participation.
- Emphasize the “Why”: Explain the potential consequences of unsafe behavior and the benefits of following safety procedures.
- Get Employees Involved: Solicit feedback from employees during the development of the training program and incorporate their expertise into the training itself.
5.2. Time Constraints
How do you deliver effective training without disrupting productivity?
- Offer Flexible Training Options: Provide online training modules that employees can complete at their own pace.
- Break Training into Smaller Sessions: Divide training into shorter, more manageable sessions to avoid overwhelming employees.
- Integrate Training into Daily Work: Incorporate safety briefings and reminders into daily work routines.
- Use Technology: Leverage online platforms and mobile apps to deliver training more efficiently.
5.3. Budget Limitations
How can you deliver effective training on a limited budget?
- Utilize Free Resources: Take advantage of free safety training resources offered by OSHA, NIOSH, and other organizations.
- Partner with Local Colleges or Training Providers: Explore partnerships with local colleges or training providers to access affordable training programs.
- Train the Trainer: Train a few employees to become safety trainers and deliver training to their colleagues.
- Leverage Technology: Utilize online platforms and mobile apps to reduce the costs associated with in-person training.
Construction Safety Training
6. Creating a Culture of Safety
How do you foster a workplace culture that prioritizes safety?
Effective safety training is just one component of creating a culture of safety. To truly foster a workplace that prioritizes safety, you need to implement a comprehensive approach that includes leadership commitment, employee involvement, and continuous improvement.
6.1. Leadership Commitment
How important is leadership support for safety initiatives?
- Set the Tone from the Top: Leaders must demonstrate a strong commitment to safety and communicate its importance to all employees.
- Allocate Resources: Provide adequate resources for safety training, equipment, and programs.
- Hold Managers Accountable: Ensure managers are held accountable for implementing safety procedures and enforcing safety rules.
- Lead by Example: Leaders should model safe behaviors and practices in their own work.
6.2. Employee Involvement
How can you encourage employees to take ownership of safety?
- Solicit Feedback: Ask employees for their input on safety policies and procedures.
- Involve Employees in Safety Committees: Create safety committees that include employees from all levels of the organization.
- Encourage Reporting: Encourage employees to report hazards and incidents without fear of reprisal.
- Recognize and Reward Safe Behaviors: Acknowledge and reward employees who consistently demonstrate safe work practices.
6.3. Continuous Improvement
How do you ensure your safety program remains effective over time?
- Regularly Evaluate Performance: Track safety metrics such as incident rates, near misses, and employee participation in safety programs.
- Identify Areas for Improvement: Analyze data to identify trends and areas where safety performance can be improved.
- Implement Corrective Actions: Develop and implement corrective actions to address identified deficiencies.
- Continuously Update Training: Regularly review and update training materials and delivery methods to ensure they remain relevant and effective.
7. The Role of CARDIAGTECH.NET in Enhancing Safety Training
How can CARDIAGTECH.NET help you conduct occupational safety training sessions for employees?
CARDIAGTECH.NET offers a range of high-quality tools and equipment that can enhance safety training programs and improve workplace safety. Our products are designed to meet the specific needs of the automotive repair industry, providing technicians with the tools they need to work safely and efficiently.
7.1. Diagnostic Tools
How can diagnostic tools improve safety in automotive repair?
CARDIAGTECH.NET provides advanced diagnostic tools that help technicians accurately identify and diagnose vehicle problems, reducing the risk of accidents and injuries. These tools include:
- OBD-II Scanners: Diagnose engine and transmission issues to prevent breakdowns and accidents.
- Brake System Analyzers: Ensure brakes are functioning properly to prevent collisions.
- Tire Pressure Monitoring Systems (TPMS) Tools: Maintain optimal tire pressure for improved handling and safety.
7.2. Protective Gear and Equipment
What types of protective gear and equipment does CARDIAGTECH.NET offer?
CARDIAGTECH.NET offers a wide range of protective gear and equipment designed to keep technicians safe while working on vehicles. Our products include:
- Safety Glasses: Protect eyes from flying debris and chemicals.
- Gloves: Protect hands from cuts, abrasions, and chemical exposure.
- Respirators: Protect lungs from harmful fumes and particles.
- Work Boots: Provide foot protection and slip resistance.
7.3. Training Resources
Does CARDIAGTECH.NET provide any training resources for its products?
CARDIAGTECH.NET offers a variety of training resources to help technicians use our products safely and effectively. These resources include:
- Product Manuals: Detailed instructions on how to use our tools and equipment.
- Online Tutorials: Step-by-step videos demonstrating proper usage and maintenance.
- On-Site Training: Hands-on training sessions conducted by experienced professionals.
- Safety Seminars: Workshops and seminars on the latest safety practices and regulations.
By partnering with CARDIAGTECH.NET, you can enhance your safety training program and create a safer, more productive work environment for your employees.
8. Legal and Regulatory Requirements for Safety Training
What are the legal requirements for safety training in the workplace?
Occupational safety training is not just a best practice; it’s often a legal requirement. OSHA and other regulatory agencies mandate specific training programs for certain industries and hazards.
8.1. OSHA Requirements
What are some common OSHA training requirements?
- Hazard Communication: Training on the hazards of chemicals in the workplace. OSHA requires employers to provide employees with information and training on hazardous chemicals in their work area at the time of their initial assignment and whenever a new hazard is introduced.
- Lockout/Tagout: Training on procedures for controlling hazardous energy during maintenance and servicing of equipment.
- Confined Space Entry: Training on the hazards of working in confined spaces and proper entry procedures.
- Fall Protection: Training on the use of fall protection equipment and procedures.
8.2. State and Local Regulations
Are there any state-specific safety training requirements?
In addition to federal regulations, many states and local jurisdictions have their own safety training requirements. It’s important to be aware of and comply with all applicable regulations in your area. For example, California has specific requirements for workplace violence prevention training in the healthcare industry.
8.3. Consequences of Non-Compliance
What are the potential penalties for failing to comply with safety training regulations?
Failure to comply with safety training regulations can result in significant fines, legal penalties, and reputational damage. OSHA can issue citations for violations of its standards, with penalties ranging from thousands to hundreds of thousands of dollars. In addition, companies that fail to comply with safety regulations may face lawsuits from injured employees and their families.
Address: 276 Reock St, City of Orange, NJ 07050, United States
Whatsapp: +1 (641) 206-8880
Website: CARDIAGTECH.NET
9. Measuring the ROI of Safety Training
How do you determine if your safety training program is paying off?
Measuring the return on investment (ROI) of safety training can be challenging, but it’s important to assess the effectiveness of your program and justify your investment. Here are some key metrics to track:
9.1. Incident Rates
How can tracking incident rates help measure training effectiveness?
- Track the Number of Accidents and Injuries: Monitor the number of workplace accidents and injuries before and after implementing safety training.
- Calculate Incident Rates: Calculate incident rates per employee or per hours worked to account for changes in workforce size or hours worked.
- Compare to Industry Benchmarks: Compare your incident rates to industry benchmarks to see how your safety performance compares to your peers.
9.2. Workers’ Compensation Costs
How can you assess the impact of training on workers’ compensation expenses?
- Track Workers’ Compensation Claims: Monitor the number and cost of workers’ compensation claims before and after implementing safety training.
- Calculate Workers’ Compensation Costs per Employee: Calculate workers’ compensation costs per employee to account for changes in workforce size.
- Compare to Industry Averages: Compare your workers’ compensation costs to industry averages to see how your safety performance compares to your peers.
9.3. Employee Morale and Engagement
How can you measure the impact of safety training on employee attitudes?
- Conduct Employee Surveys: Administer surveys to assess employee attitudes towards safety and their perception of the company’s commitment to safety.
- Track Employee Turnover: Monitor employee turnover rates to see if safety training has a positive impact on employee retention.
- Monitor Employee Participation in Safety Programs: Track employee participation in safety committees, training sessions, and other safety-related activities.
10. The Future of Occupational Safety Training
What are some emerging trends in safety training?
The field of occupational safety training is constantly evolving, with new technologies and approaches emerging to improve the effectiveness of training programs. Here are some key trends to watch:
10.1. Personalized Learning
How will personalized learning shape safety training programs?
- Adaptive Learning Platforms: These platforms use algorithms to tailor training content to each employee’s individual learning style and knowledge level.
- Microlearning: This approach involves delivering training in short, focused bursts that are easy to digest and remember.
- Gamification: Incorporating game-like elements into training can make it more engaging and motivating for employees.
10.2. Remote Training and Virtual Reality
How will technology continue to transform safety training delivery?
- Remote Training: As remote work becomes more common, remote training solutions will become increasingly important.
- Virtual Reality (VR): VR can create immersive training experiences that allow employees to practice safety procedures in realistic scenarios.
- Augmented Reality (AR): AR can overlay digital information onto the real world, providing employees with real-time safety guidance and instructions.
10.3. Data Analytics and Predictive Modeling
How can data be used to improve safety training outcomes?
- Data Analytics: Analyzing safety data can help identify trends and patterns that can be used to improve training programs.
- Predictive Modeling: Predictive modeling can be used to identify employees who are at high risk of injury and provide them with targeted training and interventions.
- Real-Time Monitoring: Real-time monitoring of workplace conditions and employee behaviors can help identify potential hazards and prevent accidents before they occur.
By staying abreast of these trends and incorporating them into your safety training program, you can create a safer, more productive work environment for your employees.
FAQ: Occupational Safety Training Sessions for Employees
1. What is occupational safety training?
Occupational safety training teaches employees how to identify workplace hazards, reduce risks, and prevent accidents, enhancing workplace safety and health.
2. Why is occupational safety training important for employees?
It reduces workplace accidents and injuries, increases productivity, improves employee morale, and ensures compliance with safety regulations, contributing to a safer work environment.
3. What topics should be covered in occupational safety training?
Training should cover hazard identification, risk assessment, emergency procedures, proper use of equipment, and relevant safety regulations specific to the workplace.
4. How often should occupational safety training be conducted?
Training frequency depends on industry regulations and workplace hazards; new employees should receive initial training, with regular refresher courses and updates as needed.
5. What are the legal requirements for occupational safety training?
Legal requirements vary by industry and location, often mandated by OSHA or similar regulatory bodies, which set standards for training content and frequency.
6. How can technology enhance occupational safety training sessions?
Online platforms, VR, AR, and mobile apps can make training more engaging, accessible, and cost-effective, providing realistic simulations and real-time updates.
7. What are the benefits of using CARDIAGTECH.NET for safety training?
CARDIAGTECH.NET offers diagnostic tools, protective gear, and training resources to enhance safety in automotive repair, reducing accidents and ensuring technician safety.
8. How can employers measure the effectiveness of occupational safety training?
Employers can track incident rates, workers’ compensation costs, and employee morale through surveys and participation rates in safety programs.
9. How can a culture of safety be fostered in the workplace?
Leadership commitment, employee involvement, continuous improvement, and open communication are key to fostering a workplace culture that prioritizes safety.
10. What are some emerging trends in occupational safety training?
Personalized learning, remote training, VR, AR, data analytics, and predictive modeling are emerging trends that enhance the effectiveness and accessibility of safety training programs.
CARDIAGTECH.NET understands that your team may have specific questions about implementing or enhancing your safety training programs. Don’t hesitate to reach out to us at +1 (641) 206-8880 or visit CARDIAGTECH.NET for expert guidance and solutions tailored to your needs.