Do You Have Contingency Plans for Disruptions in the Supply of Spare Parts?
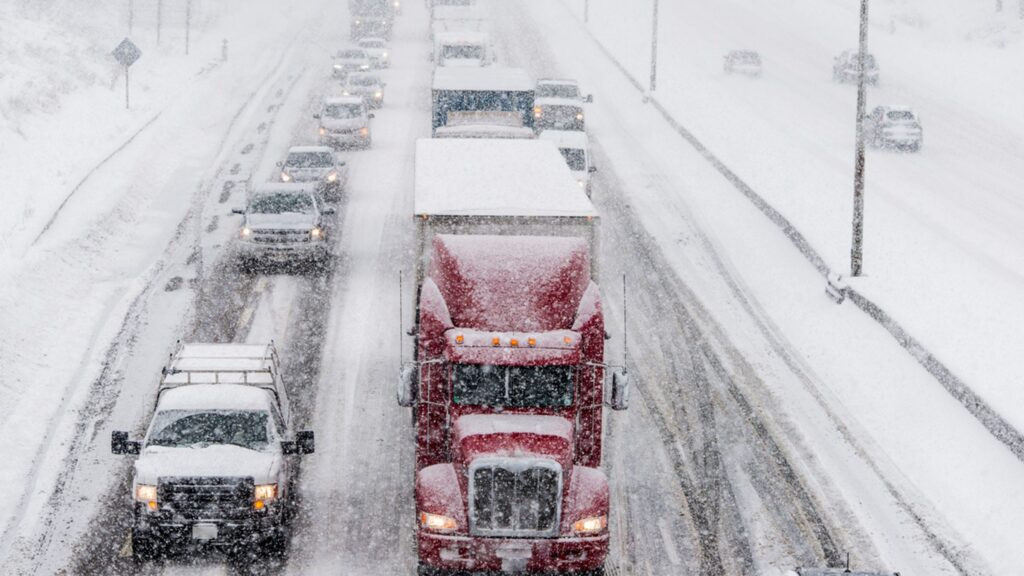
Are you prepared for unexpected disruptions in your spare parts supply chain? CARDIAGTECH.NET understands the critical importance of having robust contingency plans to minimize downtime and maintain operational efficiency in your auto repair shop. Discover how to proactively address potential disruptions and keep your business running smoothly with our expert guidance and cutting-edge diagnostic tools. Learn about risk mitigation strategies, alternative sourcing, and inventory management solutions to safeguard your business.
1. Understanding the Criticality of Contingency Plans for Spare Parts
Do you know why contingency plans are crucial for managing spare parts supply chain disruptions? Contingency plans are essential because they provide a structured approach to dealing with unexpected events, ensuring minimal disruption to your operations. According to a study by the Economist Impact, supply chain slowdowns can cost companies 6-10% of their annual revenue, underscoring the financial impact of unpreparedness. Having a contingency plan enables your auto repair shop to quickly adapt to challenges, maintain customer satisfaction, and protect your bottom line.
1.1. The Role of Contingency Plans
What role do contingency plans play in mitigating supply chain risks for spare parts? Contingency plans outline specific actions to take when disruptions occur, such as sourcing from alternative suppliers, expediting shipments, or adjusting production schedules. By having these strategies in place, you can minimize delays and ensure a continuous supply of critical spare parts.
1.2. Financial Impact of Supply Chain Disruptions
How do spare parts supply chain disruptions affect your business financially? Disruptions can lead to lost revenue due to production slowdowns and delivery delays, as well as increased costs from expedited shipping and alternative sourcing. Effective contingency plans can help mitigate these financial impacts by ensuring business continuity and minimizing downtime.
2. Common Disruptions Affecting Spare Parts Supply Chains
What are the common disruptions that can affect your spare parts supply chain? Supply chains are vulnerable to a range of disruptions, from natural disasters and economic instability to operational issues and geopolitical events. Being aware of these potential disruptions is the first step in developing effective contingency plans.
2.1. Natural Disasters
How can natural disasters impact the supply of spare parts? Natural disasters like hurricanes, earthquakes, and floods can severely disrupt logistics and operations, leading to delays and shortages. Hurricane Katrina, for instance, caused $125 billion in economic losses and significantly disrupted supply chains across multiple industries, highlighting the potential devastation.
Supply Chain Disruption Caused by Blizzard
2.2. Economic, Infrastructure, and Political Factors
What economic, infrastructure, and political factors can disrupt spare parts supply chains? Tariffs, trade wars, political instability, and infrastructure failures (such as the Baltimore bridge collapse) can create significant disruptions. These factors can alter trade routes, cut off material suppliers, increase costs, and necessitate adjustments in supply chain strategies. According to CNBC, Southeast Asia is a top choice for firms diversifying away from China, indicating the impact of geopolitical disruptions on sourcing decisions.
2.3. Operational Issues
How do internal operational issues affect spare parts availability? Inefficient processes, machinery breakdowns, labor strikes, and poor warehouse management can all lead to delays and shortages. Automating internal processes and implementing effective management protocols can help minimize these internal risks.
3. Key Components of an Effective Contingency Plan for Spare Parts
What are the essential elements of a robust contingency plan for managing spare parts supply chain disruptions? A comprehensive contingency plan should include risk assessment, alternative sourcing strategies, inventory management, communication protocols, and continuous improvement processes. These components work together to ensure your business can quickly respond to and recover from disruptions.
3.1. Risk Assessment
Why is risk assessment a critical first step in developing a contingency plan? Risk assessment involves identifying potential disruptions and evaluating their likelihood and impact. This allows you to prioritize risks and develop targeted mitigation strategies.
3.2. Alternative Sourcing Strategies
What alternative sourcing strategies can you implement to secure your spare parts supply? Developing relationships with multiple suppliers and exploring nearshoring options can reduce your reliance on a single source and minimize the impact of disruptions.
3.3. Inventory Management
How can effective inventory management help mitigate spare parts shortages? Maintaining safety stocks and implementing inventory management systems can ensure you have enough spare parts on hand to meet demand during disruptions.
3.4. Communication Protocols
Why are clear communication protocols essential during a supply chain disruption? Clear communication with suppliers, customers, and employees can help manage expectations, minimize frustration, and ensure everyone is informed about the situation and the steps being taken to address it.
3.5. Continuous Improvement
How can continuous improvement enhance your contingency planning? Regularly reviewing and updating your contingency plans based on past experiences and new risks can ensure they remain effective and relevant.
4. Steps to Take When a Spare Parts Supply Chain Disruption Occurs
What steps should you take when a disruption impacts your spare parts supply chain? When a disruption occurs, it’s essential to assess the situation, activate your contingency plan, communicate effectively, prioritize critical needs, explore alternative solutions, and adapt as the situation evolves.
4.1. Assess the Situation
How do you effectively assess the impact of a supply chain disruption? Gather as much information as possible about the nature of the disruption, its root cause, the specific parts of your supply chain that are impacted, and the potential duration of the issue.
4.2. Activate Your Contingency Plan
What does activating your contingency plan entail? This involves implementing the pre-defined steps outlined in your plan, such as contacting backup suppliers, expediting shipments, or adjusting production schedules.
4.3. Communicate Effectively and Clearly
Why is communication paramount during a disruption? Keep all stakeholders informed, including customers, suppliers, and employees. Be transparent about the situation and the steps you are taking to address it. Regular communication helps to manage expectations and minimize frustration.
4.4. Prioritize Critical Needs
How do you prioritize your critical needs during a disruption? Identify your most critical needs and focus your resources on getting those products through logistics first. Take stock of your warehouse inventory and the location of goods across your network. You may need to ration inventory or reallocate resources strategically to triage identified needs.
4.5. Explore Alternative Solutions
What alternative solutions can you explore to maintain your spare parts supply? Think creatively and look for alternative solutions to keep your part of the supply chain moving despite disruption. This could involve finding new suppliers, using different transportation routes, or even redesigning products to use alternative materials.
4.6. Adapt and Mitigate
How do you adapt your approach as the situation evolves? Be prepared to adapt your approach as the situation evolves. The goal is to mitigate the impact of the disruption as much as possible and get your supply chain back on track.
5. Building a Resilient Spare Parts Supply Chain Network
What strategies can you employ to build a more resilient spare parts supply chain? Building a resilient supply chain requires proactive measures, such as developing contingency plans, building safety stocks, considering nearshoring, and leveraging forecasting and technology.
5.1. Develop Contingency Plans
Why are detailed contingency plans the cornerstone of a resilient supply chain? An effective contingency plan should include clear steps for managing disruptions, maintaining operations, and communicating with stakeholders.
5.2. Build Safety Stocks
How do safety stocks provide a buffer against disruptions? Safety stocks act as a buffer against supply chain disruptions. Increasing your stock and supply chain visibility helps keep your business ahead of customer demand so you’re never caught in short supply.
5.3. Consider Nearshoring Your Supply Chain
What are the benefits of nearshoring for spare parts supply? Nearshoring involves moving manufacturing to a close-by country, which can reduce the risks associated with long-distance shipping and supply chain networks. According to Flat World Global Solutions, a typical transport from Mexico to the U.S. might only take a quarter of the time it would take to ship that same inventory from China, and cost a lot less money.
5.4. Leverage Forecasting and Technology
How can technology enhance your ability to manage supply chain disruptions? Leveraging digital tools and other technology for predicting disruptions and conducting vulnerability assessments is crucial. Accurate forecasting helps businesses anticipate potential supply chain shocks and take preemptive action. Flat World’s Pipeline TMS (transportation management system) offers a 360° view of your entire supply chain data.
6. The Importance of Partnering with a Reliable Supplier Like CARDIAGTECH.NET
Why is choosing the right supplier crucial for managing spare parts supply chain disruptions? Supply chain disruptions are inevitable, but companies can mitigate their impact through proactive measures, robust contingency plans, and strong partnerships. By learning from past disruptions and leveraging technology, businesses can build more resilient supply chains that can withstand future challenges and any potential disruption.
Warehouse Logistics Partnership
6.1. Enhancing Operational Efficiency
How does CARDIAGTECH.NET enhance your operational efficiency? CARDIAGTECH.NET offers a wide range of high-quality diagnostic tools and spare parts, ensuring you have the resources you need to keep your auto repair shop running smoothly. Our products are designed to improve accuracy, reduce repair times, and minimize downtime.
6.2. Ensuring Market Responsiveness
How does CARDIAGTECH.NET help you stay responsive to market demands? By partnering with CARDIAGTECH.NET, you gain access to a reliable supply of spare parts and cutting-edge technology, allowing you to quickly adapt to changing market demands and customer needs.
7. Real-World Examples of Successful Contingency Planning
Can you provide examples of companies that have successfully navigated spare parts supply chain disruptions through effective contingency planning? Many companies have successfully mitigated the impact of disruptions by implementing robust contingency plans. For instance, during the COVID-19 pandemic, companies that had diversified their supply base and invested in inventory management systems were better able to maintain operations and meet customer demand.
7.1. Case Study 1: Automotive Manufacturer
How did one automotive manufacturer successfully navigate a supply chain disruption? An automotive manufacturer facing a shortage of semiconductors due to a natural disaster in Taiwan quickly activated its contingency plan. The plan included sourcing from alternative suppliers in other regions, redesigning certain components to use more readily available parts, and communicating transparently with customers about potential delays. As detailed by industry analysts at Deloitte, the manufacturer minimized the impact on production and maintained customer satisfaction by proactively managing the disruption.
7.2. Case Study 2: Electronics Retailer
How did an electronics retailer mitigate disruptions during a trade war? An electronics retailer anticipated potential disruptions from a trade war by increasing its safety stock of critical components and diversifying its supplier base to include manufacturers in multiple countries. When tariffs were imposed on certain goods, the retailer was able to shift its sourcing to avoid the tariffs and maintain competitive pricing, a move praised by supply chain experts at Gartner.
8. Leveraging Technology for Enhanced Contingency Planning
How can technology improve your contingency planning and response to spare parts supply chain disruptions? Technology plays a crucial role in enhancing contingency planning by providing tools for risk assessment, forecasting, inventory management, and communication.
8.1. Risk Assessment Tools
What types of risk assessment tools are available to help you identify potential disruptions? Risk assessment tools can help you identify potential disruptions and evaluate their likelihood and impact, allowing you to prioritize risks and develop targeted mitigation strategies.
8.2. Forecasting Software
How can forecasting software improve your ability to anticipate disruptions? Forecasting software can help you anticipate potential supply chain shocks and take preemptive action by analyzing historical data and identifying trends.
8.3. Inventory Management Systems
How do inventory management systems contribute to effective contingency planning? Inventory management systems can help you maintain optimal inventory levels and track the location of spare parts across your network, ensuring you have enough stock on hand to meet demand during disruptions.
8.4. Communication Platforms
How do communication platforms facilitate rapid response during a disruption? Communication platforms can facilitate rapid communication with suppliers, customers, and employees, allowing you to quickly share information and coordinate your response to a disruption.
9. Proactive Measures to Minimize Spare Parts Supply Chain Risks
What proactive measures can you take to minimize the risks to your spare parts supply chain? In addition to developing contingency plans, you can take proactive measures such as diversifying your supply base, building strong relationships with suppliers, and investing in cybersecurity.
9.1. Diversifying Your Supply Base
Why is diversification a key strategy for minimizing supply chain risks? Diversifying your supply base reduces your reliance on a single source and minimizes the impact of disruptions.
9.2. Building Strong Relationships with Suppliers
How can strong supplier relationships enhance your supply chain resilience? Building strong relationships with suppliers can improve communication, collaboration, and trust, making it easier to work together to address disruptions.
9.3. Investing in Cybersecurity
Why is cybersecurity an important aspect of supply chain risk management? Cybersecurity is essential for protecting your supply chain from cyberattacks, which can disrupt operations and compromise sensitive information.
10. Partnering with CARDIAGTECH.NET for Your Diagnostic Tool Needs
Why should you choose CARDIAGTECH.NET as your trusted supplier of diagnostic tools and spare parts? CARDIAGTECH.NET is committed to providing high-quality products, reliable service, and expert support to help you manage your auto repair shop efficiently and effectively.
10.1. Wide Range of Diagnostic Tools
What diagnostic tools does CARDIAGTECH.NET offer to support your business? CARDIAGTECH.NET offers a wide range of diagnostic tools to help you accurately diagnose and repair vehicles, reducing downtime and improving customer satisfaction.
10.2. Reliable Supply of Spare Parts
How does CARDIAGTECH.NET ensure a reliable supply of spare parts? CARDIAGTECH.NET maintains a robust inventory of spare parts and works with trusted suppliers to ensure you have access to the parts you need, when you need them.
10.3. Expert Support and Training
What support and training does CARDIAGTECH.NET provide to help you maximize the value of your diagnostic tools? CARDIAGTECH.NET offers expert support and training to help you effectively use our diagnostic tools and troubleshoot issues, ensuring you get the most out of your investment.
FAQ: Contingency Plans for Spare Parts Supply
1. What is a contingency plan in the context of spare parts supply?
A contingency plan is a proactive strategy that outlines steps to manage and mitigate potential disruptions in the supply of spare parts, ensuring business continuity.
2. Why is it important to have contingency plans for spare parts?
Contingency plans minimize downtime, maintain operational efficiency, and protect your bottom line by providing alternative solutions when disruptions occur.
3. What are common disruptions that can affect spare parts supply?
Common disruptions include natural disasters, economic instability, political factors, operational issues, and supplier failures.
4. How can risk assessment help in developing a contingency plan?
Risk assessment identifies potential disruptions and evaluates their likelihood and impact, allowing you to prioritize risks and develop targeted mitigation strategies.
5. What are some alternative sourcing strategies for spare parts?
Alternative sourcing strategies include developing relationships with multiple suppliers, nearshoring, and using different transportation routes.
6. How does inventory management play a role in contingency planning?
Effective inventory management ensures you have enough spare parts on hand to meet demand during disruptions, minimizing downtime and lost revenue.
7. What should be included in communication protocols during a supply chain disruption?
Communication protocols should include clear and transparent communication with suppliers, customers, and employees, keeping everyone informed about the situation and the steps being taken to address it.
8. How can technology enhance contingency planning for spare parts?
Technology provides tools for risk assessment, forecasting, inventory management, and communication, improving your ability to anticipate and respond to disruptions.
9. What proactive measures can be taken to minimize supply chain risks?
Proactive measures include diversifying your supply base, building strong relationships with suppliers, and investing in cybersecurity.
10. Why is partnering with a reliable supplier like CARDIAGTECH.NET beneficial?
Partnering with CARDIAGTECH.NET ensures you have access to high-quality diagnostic tools, a reliable supply of spare parts, and expert support, helping you manage your auto repair shop efficiently and effectively.
Don’t let unexpected disruptions derail your auto repair business. Contact CARDIAGTECH.NET today at 276 Reock St, City of Orange, NJ 07050, United States, or call us on WhatsApp at +1 (641) 206-8880 to learn how our diagnostic tools and reliable spare parts supply can help you build a resilient supply chain. Visit our website at CARDIAGTECH.NET to explore our full range of products and services. Let us help you keep your business running smoothly, no matter what challenges you face!